جوشکاری زیر پودری چیست؟
مشابه فرایند جوشکاری MIG، جوشکاری زیرپودری نیز مستلزم تشکیل قوس بین قطعه کار و یک الکترود سیمی بدون پوشش که به طور مداوم پایین میآید می باشد. فرایند SAW از یک فلاکس جهت تولید گازها و سرباره محافظ و همچنین افزودن عناصر آلیاژی به حوضچه ذوب استفاده میکند. در این روش، گاز محافظ لازم نیست. جنس سیم جوش در جوشکاری زیر پودری، از جنس فولادی زنگ نزن با روکش مس میباشد. روکش مسی انتقال جریان الکتریکی را سرعت می بخشد. در ادامه با آموزش جوشکاری زیرپودری در خدمت شما هستیم.
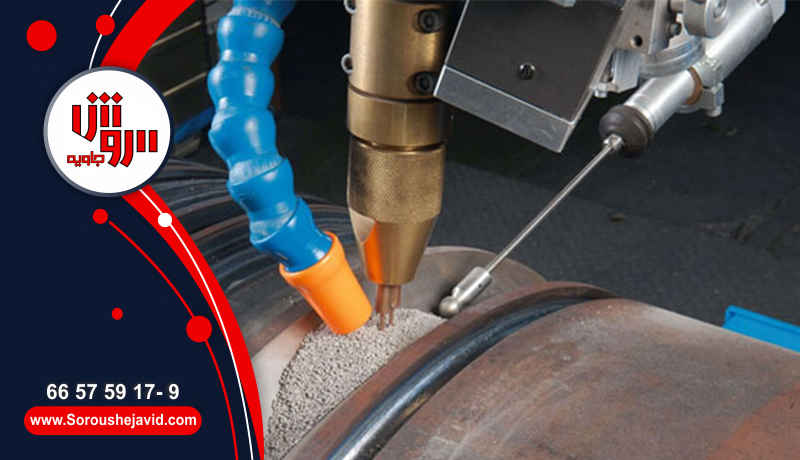
دلیل استفاده از فولاد زنگ نزن، سهولت نگهداری از سیم جوش در انبار است. سیمهای جوش باید عاری از هر نوع آلودگی باشند و سطحی پاک و تمیز داشته باشند.
مزایای جوشکاری زیرپودری (SAW)
از آنجا که در این روش به جای جوشکار، از متصدی دستگاه جوشکاری استفاده میشود، کیفیت جوش حاصله از مهارت جوشکار و همچنین خطاهای انسانی مستقل است. بیشترین نرخ رسوب در میان فرآیندهای جوشکاری ذوبی به روش زیرپودری اختصاص دارد که به سرعت بالای جوشکاری منجر میگردد. در این روش به پوشش برای حفاظت اپراتور از قوس نیاز نیست، اگرچه حفاظت چشمان اپراتور بخاطر احتمال پرتاب جرقه حاصل از جوش توصیه می شود. ذرات فلاکس (پودر دانهای) نسبت به روکش الکترود در جوشکاری دستی، حفاظت بهتر و بیشتری از نوار جوش انجام میدهد.
محدودیتهای استفاده از روش جوشکاری زیرپودری
• تجهیزات این روش بسیار پیچیده و گران است.
• در کاربردهای خاص شدیدا مسطح بودن وضعیت جوشکاری اهمیت دارد، زیرا مسطح بودن و افقی بودن وضعیت برای جلوگیری از ریختن فلاکس لازم است.
• پودر جوش ممکن است به آلودگیهایی آغشته باشد که باعث تخلخل در جوش شوند.
• جدا شدن سرباره از جوش در بعضی موارد به سختی صورت می گیرد.
• در جوش های چند پاسه، پس از هر عبور نیاز است سرباره جوش برداشته شود تا از باقی ماندنش درون فلز جوش جلوگیری شود.
وسایل و تجهیزات جوشکاری زیرپودری (SAW)
تجهیزات لازم برای اجرای جوش زیرپودری (SAW) عبارتند از:
• مولد
• مخزن پودر
• نازل پودر
• انبر
• سیستم نگهداری و هدایت الکترود بدون پوشش
• روبات هدایت انبر و ریلهای مربوط به آن
فلزات مناسب جوشکاری زیرپودری SAW
جوش زیر پودری برای همه فلزات و آلیاژها مناسب نمیباشد. برای سهولت ، فلزات و آلیاژها را میتوان با توجه به مناسب بودن آنها برای جوشکاری زیرپودری ،به سه دسته کلی تقسیم کرد:
فلزات بسیارمناسب
فلزات اندکی مناسب
فلزات غیرمناسب
فلزات بسیار نامناسب
فلزات اندکی مناسب
برخی فلزات و آلیاژهایی را که میتوان به روش جوشکاری زیرپودری جوش داد، بیشتر با روشهایی جوش میدهند که منطقه حرارت داده شده باریکتر باشد. برخی فولادهای ساختمانی پراستحکام و کم کربن جزء این گروه هستند زیرا استحکام و کشش مورد نیاز در روش جوشکاری زیرپودری ( SAW )به سختی بدست میآیند.فولادهای پرکربن، فولادهای مار تنزیتی، مس و آلیاژهای مس نیز جزء این گروه محسوب میشوند.
فلزات نامناسب
معمولا چدن را نمیتوان به روش جوشکاری زیرپودری جوش داد، زیرا نمیتواند تنشهای حرارتی ناشی از گرمای ورودی را تحمل کند. مواردی که در جوش فولاد آستنیته منگنزی و فولاد ابزار پرکربن رخ میدهند جوشکاری آنها را با هر روش معمولی دشوار میسازد.آلیاژهای آلومینیوم و آلیاژهای منیزیوم را نمیتوان به روش زیر پودری جوش داد چرا که فلاکس مناسب برای آن پیدا نمیشود. سرب و روی بخاطر نقطه ذوب پایین ، مناسب جوشکاری زیرپودری SAW نمیباشند. تیتانیوم در کاربردهای آزمایشگاهی به روش زیر پودری جوشکاری شده است، ولی فلاکس مناسب برای جوش آن تاکنون ارائه نشده است.
عوامل موثر بر جوش زیرپودری
اکنون که با چگونگی جوشکاری زیر پودری آشنا شدیم به بررسی عوامل موثر بر کیفیت جوش زیر پودری خواهیم پرداخت.
جریان الکتریکی
جریانی با قطبیت معکوس(DCEP) عمق جوش کم و جریانی با قطبیت مستقیم(DCEP) عمق جوش زیاد ایجاد میکند. در صنایع مختلف بیشتر از جریان با قطبیت معکوس و قطر کم استفاده میشود. چون بازیابی عناصر آسانتر و مقدار اکسیداسیون کمتر است.
ولتاژ
هرچه ولتاژ افزایش یابد، گرده جوش پهنتر، سطح جوش مسطحتر و عمق جوش نیز کمتر میشود. اگر فلز جوشکاری بیشتر از مقدار مورد نیاز برای پر کردن محل اتصال باشد، گرده جوش ایجاد میشود.
سرعت جوشکاری
با افزایش سرعت جوشکاری، زمان جوشکاری کاهش مییابد. سرعت زیاد علاوه بر کاهش حرارت ورودی، میتواند پهنا و عمق جوش را نیز کم کند. این مسئله منجر به لاغر شدن گرده جوش خواهد شد.
سیم جوش
ترکیب شیمیایی سیم جوش بر خاصیت نهایی جوش موثر است. علاوه بر این شکل مقطع جوش نیز بر کیفیت جوشکاری تاثیر میگذارد. در صورتیکه مقطع الکترود گرد باشد، با کاهش قطر عمق نفوذ جوش افزایش خواهد یافت.
طول موثر الکترود
به فاصله محل اتصال برق به الکترود تا محل اتصال سیم الکترود به قطعه کار طول موثر الکترود گفته میشود. هر چه طول موثر الکترود بیشتر باشد، نرخ رسوب نیز افزایش مییابد. زیرا مقدار مقاومت و به دنبال آن حرارت تولید شده افزایش پیدا میکند. همچنین افزایش این طول موثر باعث کاهش عمق نفوذ جوش نیز میشود.
پودر فلاکس
برای داشتن مواد مذاب باکیفیتتر در حوضچه جوش، بایستی میزان ترکیب قلیایی پودر در جوش زیرپودری بیشتر باشد. از جمله پودرهای مورد استفاده در جوش زیرپودری لوله شامل سیلیکات منگنز، سیلیکات کلسیم، سیلیکات زیرکونیوم، سیلیکات روتیلی، سیلیکات زیرکونیوم، پودر فلورید قلیایی، پودر آهن، پودر آلومینات روتیلی و آلومینات سیلیکات میشود.
سخن آخر
جوشکاری الکترود دستی (SMAW) به رغم قدمت و کاربرد فراوانی که دارد، برای فرد جوشکار مشکلاتی را در حین جوشکاری ایجاد میکند که از جمله این مشکلات میتوان به پاشش مواد مذاب، تابش اشعه خطرناک ماوراء بنفش و آلودگیهای جوی و زیستمحیطی که در هنگام کار ایجاد میشود اشاره کرد. به همین دلیل روش جدیدی به نام جوشکاری زیر پودری (SAW) در جوشکاری تعریف شده است که این مشکلات را برطرف میکند. امروزه این روش به خصوص برای سازههای سنگین فولادی و تولیدات انبوه نظیر جوشکاری بدنه کشتیها و مخازن کاربردهای زیادی دارد. در این مقاله از سروش جاوید با ساز و کار این روش و محدودیتهای آن آشنا شدیم و مزایا و معایب این روش را بررسی نمودیم. از اینکه تا پایان این مطلب با ما همراه بودید از شما کمال تشکر را داریم و امیدواریم این مطلب برای شما مفید واقع شده باشد.